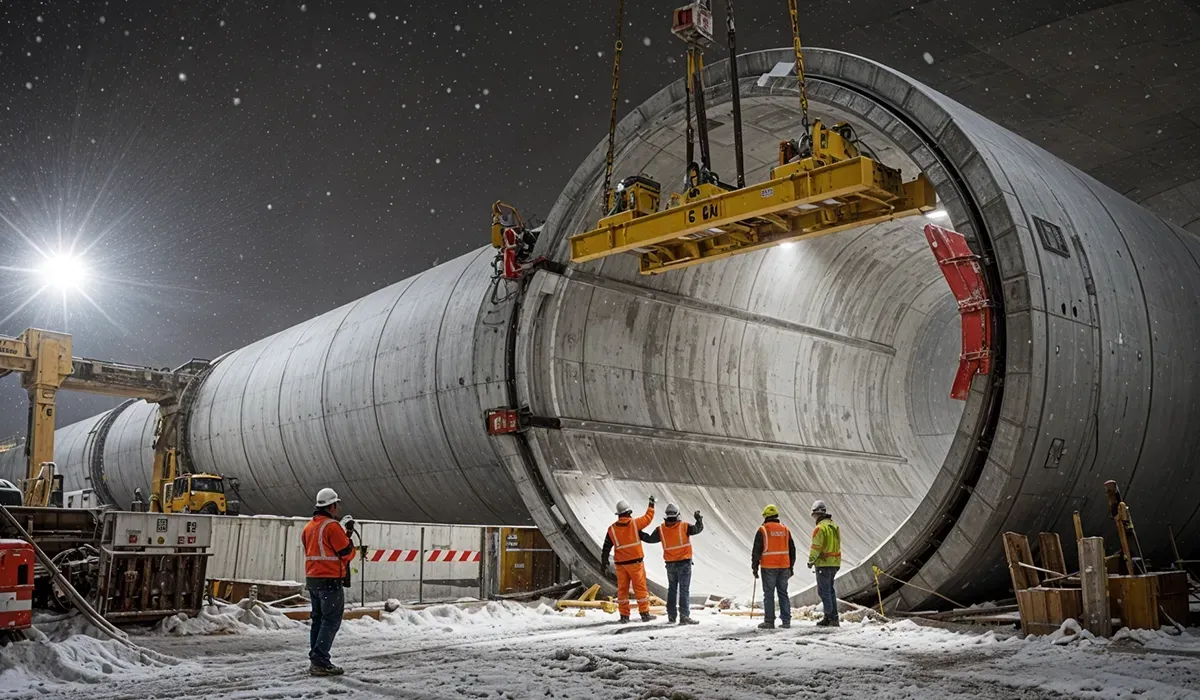
Innovative Precast Design Techniques for Faster and Stronger Structures
Speed and strength are two things every project manager wants more of but rarely gets together. In modern construction, delays are expensive, and structural compromise is never an option.
That is where innovation in precast design techniques starts pulling weight. We are not talking about cutting corners. We are talking about innovative, factory-led thinking that transforms how buildings come together—stronger, faster, and cleaner.
This is not just about staying ahead of the curve. It is about making the curve yours. As the industry shifts towards efficiency and performance, those sticking to the same old formulas risk falling behind. The real win? Adopting design strategies that don’t just build faster—but build better.
If you have ever wondered what separates a good project from a game-changer, this deep dive into innovative precast design techniques will give you that edge.
1. From Conventional to Cutting-Edge: Why Precast Design Needs a Rethink
Old-school methods still get the job done—but do they do it well enough? Not really.
When project schedules are tight, and quality expectations are high, relying on traditional layouts and production routines can feel like driving with the handbrake on. More teams are turning to precast concrete solutions engineered from the ground up for speed and structural integrity.
The big shift? Thinking beyond slab and beam. Today’s precast design techniques embrace complexity without compromising consistency. From adaptive layouts to prefabricated hybrid solutions, designers are moving toward a new mindset: optimise from the mold up. Because if the factory floor is not efficient, the site certainly will not be.
As demand grows for sustainable, high-performance builds, evolving your design approach becomes less of a luxury and more of a non-negotiable. And that’s precisely where innovation steps in—making structure smarter, systems tighter, and deadlines shorter.
2. Smart Moulding Systems and Formwork Innovation
If there is one place where a minor tweak can create a massive impact, it’s in the mold.
That’s not an exaggeration. Traditional fixed-form setups are stiff, slow, and expensive to tweak. But modular and magnetic moulding systems? They’re rewriting the playbook. These innovations in precast design techniques are turning customisation into a quick switch instead of a significant production halt.
Instead of designing around limitations, engineers now design around flexibility. With movable inserts, reusable formwork, and adaptable casting tables, precast concrete solutions can deliver intricate shapes faster and with less waste. Every repeat pour gets easier. Every design gets tighter. And the quality? Unmatched.
This is not just about looking cool on paper. These systems reduce errors, speed up cycle times, and cut costs, allowing designers to push aesthetic and functional boundaries.
When molds get smarter, everything downstream runs smoother. But that’s just one gear in the machine.
3. Seamless Connection Systems: Less Time, More Strength
Now, let us talk about joints. Connections aren’t just structural details—they are the lifelines of any precast structure. One loose end and the whole project starts to wobble. Modern precast design techniques turn these potential weak points into strengths.
Mechanical connectors, dry joints, post-tensioning systems—they are not just buzzwords. They are why today’s precast concrete solutions can deliver monolithic-like stability without waiting. By reducing the need for wet joints and heavy reinforcement on-site, projects see shorter construction timelines, fewer delays, and better control over quality.
What does this mean on the ground? Less curing time, reduced workforce, and tighter tolerances. Plus, with earthquake and wind-resistant designs becoming standard, these connections are not just faster—they are safer.
The beauty of seamless connections is that they let each piece work like part of a whole, not a patchwork. Speaking of pieces working in harmony—wait until you see what digital tools bring.
4. Parametric Design & BIM Integration: Faster from Drawing Board to Delivery
Designing in 2D? That’s like flying blind. Parametric modelling and Building Information Modeling (BIM) is changing how precast design techniques shape the real world. No more guesswork. No more back-and-forths. Just clean, data-driven decisions from start to finish.
By integrating parametric logic, teams can tweak dimensions, shapes, and loads in real-time—watching how every change affects the bigger picture. BIM goes even further. It connects designers, engineers, fabricators, and contractors under one digital roof. Everyone sees the same thing. Everyone stays on track.
This smooth collaboration means fewer RFIs, faster clash detection, and better planning from design to installation. When precast concrete solutions are looped into this digital flow, the production lines hum with precision.
Here is what ties it all together: design is no longer a static phase. It’s a dynamic engine driving every step of the build.
5. Material Science Meets Design: Leveraging UHPC & Lightweight Mixes
Let’s face it—good materials make significant structures. Today, those materials do much more than fill the mould: Ultra-high-performance concrete (UHPC) and lightweight concrete mixes open possibilities in precast design techniques.
With UHPC, you get compressive strength of up to 150 MPa. That is not a typo. It means you can go thinner and lighter and still outperform conventional elements. Add fibre reinforcement; suddenly, you are reducing steel, improving durability, and cutting down maintenance for decades.
Lightweight mixes are no slouch, either. They are ideal for high-rise projects, long-span elements, or areas with a make-or-break structural load. They are easier to transport, install quicker, and more adaptable than old-school heavyweights.
These materials are not just cool—they are game changers. When precast concrete solutions start using them right, the result is a lean, mean, and powerful product.
6. Factory-First Thinking: Designing for Production Efficiency
Here is a truth most overlooked: if it’s not designed for the factory, it won’t work on-site. Precast design techniques prioritising the production process aren’t just smarter but necessary.
When design teams think like manufacturers, everything improves. Mold reuse increases. Layouts become cleaner. And waste? It drops like a rock. From element labelling to stacking logistics, these details matter way more than people think.
The best part? The production-driven design does not just help the factory—it slashes installation time, too. When every piece comes off the line ready to fit like a puzzle, there is no fumbling on-site. No rework. No costly surprises.
Precast concrete solutions that run on this model become faster, more consistent, and more profitable. So, yeah—designing for the factory isn’t cutting corners. It’s building with your head and your hands.
7. Sustainability by Design: Greener, Smarter Structures
We can not talk about innovation without talking about green. Smarter precast design techniques also lead the charge in sustainable construction—and it’s not just about looking good on paper.
Designers now reduce cement content with mix optimisation, integrate recycled aggregates, and use carbon-capture technologies. The goal? Shrink the footprint without compromising the form. These are not just small wins. They are building blocks for long-term change.
When production becomes leaner, materials are lighter, and transport is minimised, you save costs and resources. Precast concrete solutions now offer net-zero-ready elements, which is just the start.
Sustainability is not an afterthought anymore. It’s built into the foundation—quite literally. And the best part? Going green never looked this sharp or performed this well.
Summing Up!
Here is the real takeaway—innovation in precast design techniques isn’t some future fantasy. It is happening now. And it is making structures faster, stronger, and brighter than ever.
Whether planning a modular housing project, an infrastructure upgrade, or a commercial development, aligning your strategy with forward-thinking precast concrete solutions will change the game.
The tools are here. The systems are tested. The only question is: Are you building the old or right way?