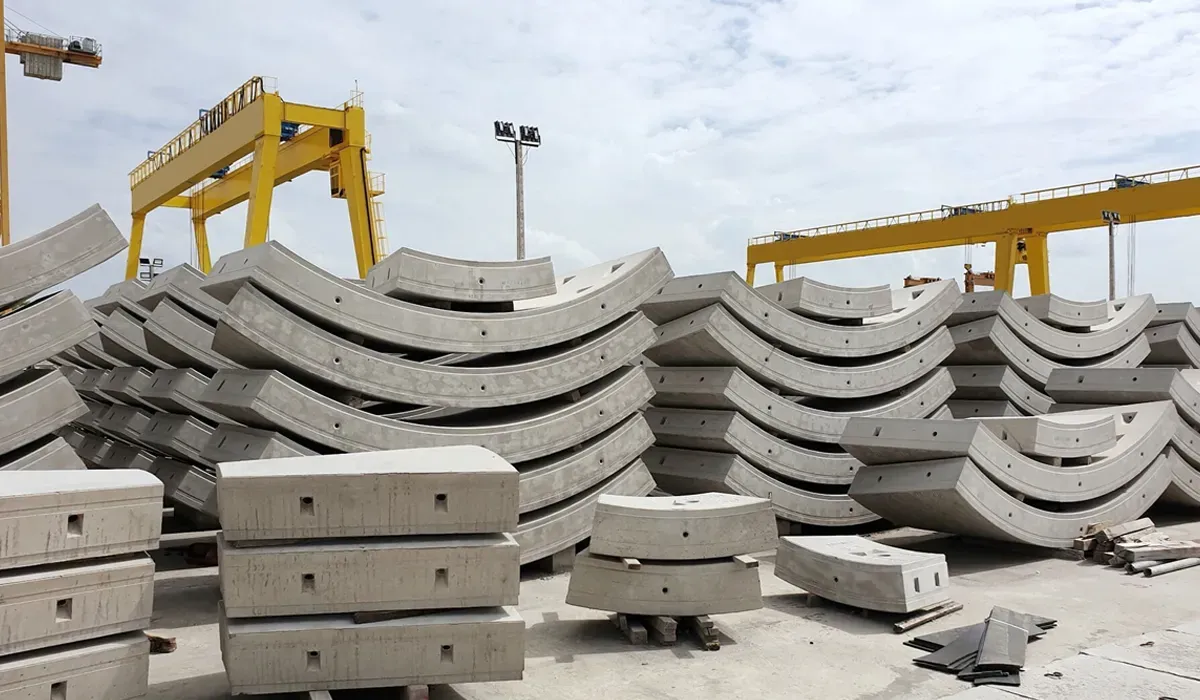
9 Emerging Trends Reshaping the Precast Concrete Industry in 2025.
The precast concrete industry is on the brink of some serious transformations.
The construction industry is at a pivotal juncture as technology develops, construction methods change, and the demand for affordable, sustainable solutions increases. For construction professionals, staying ahead of these trends can mean the difference between success and falling behind.
With evolving customer demands, tighter budgets, and the need for speed, the future of modular construction is now. In 2025, 3D printing, enhanced automation, and the global surge in infrastructure development are redefining how precast concrete products are made, delivered, and applied.
This blog will explore these exciting trends that are reshaping the industry and how they can benefit you.
1. Smart Precast Concrete: The Age of IoT Integration
The use of Internet of Things (IoT) technology in precast concrete is evolving into a revolution rather than merely a trendy term.
Contractors and facility managers can keep an eye on critical parameters like temperature, moisture content, and structural integrity in real time by integrating sensors into concrete components. Imagine being able to remotely monitor a concrete wall or beam to make sure it's functioning as intended without having to physically inspect it.
This is about making predictive maintenance more visible, not simply about making things more efficient. Precast concrete buildings can be more durable, survive longer, and require fewer maintenance thanks to this technology. The Internet of Things-enabled technologies provide quicker reaction times in the event of problems, avoiding expensive repairs and needless downtime.
With the infrastructure development, this technology can also be applied to larger-scale projects where preventative maintenance can have a significant impact. Adding smart technology makes sense as construction processes become more automated. It makes sense to incorporate smart technology as construction processes become more automated.
2. 3D Concrete Printing: The Future of Customization.
Gone are the days of only standard shapes and sizes. 3D printing is revolutionising the precast concrete industry, enabling companies to create custom-designed concrete elements with incredible precision. This level of flexibility opens up new possibilities for architects and engineers working on unique projects where traditional moulds would not work.
What makes 3D printing so exciting is its ability to reduce waste—something that is always a big concern in the construction world. With the capability to print just the material needed for each project, waste is minimised, and production becomes far more sustainable. Plus, the speed at which these structures can be printed is remarkable.
This is particularly beneficial in modular construction. Instead of waiting weeks or months for custom-made precast concrete elements, 3D printing allows parts to be ready quickly. So, whether you are working on residential buildings, commercial projects, or public infrastructure, 3D printing has the potential to streamline the process significantly.
3. Sustainable Mix Designs: The Green Shift
Sustainability is no longer optional. As concerns about climate change grow, the precast concrete industry is stepping up its game by developing greener materials and techniques. Low-carbon cement, industrial byproducts, and recycled aggregates are examples of sustainable mix designs that are gaining popularity.
The infrastructure development is significantly impacted by this tendency. By adopting more sustainable techniques, we may lessen the impact of the building industry, which is one of the largest contributors to global carbon emissions. The durability and structural integrity of conventional choices can be equaled by these environmentally friendly concrete mixes.
This strategy not only lessens environmental harm but also satisfies customers' increasing desire to lessen their carbon footprint. Green concrete is the future, and for businesses ready to innovate, it is an excellent opportunity to stand out.
4. Advanced Finishing Techniques: Where Aesthetics Meets Durability
Precast concrete is not just about strength anymore; it is also about aesthetics. With new advancements in finishing techniques, contractors can now achieve various looks, from polished surfaces to textured finishes. These finishes provide a surface that is resistant to environmental wear and tear, which not only improves longevity but also looks nice.
This trend is beautiful because it improves the shape and functionality of concrete. Precast concrete's reputation for durability can be preserved while gorgeous façade or eye-catching flooring alternatives are created with textured or polished finishes.
For modular construction, these advanced finishes save time. Pre-finished precast elements are manufactured in a controlled environment and shipped directly to the site, ready for installation. This eliminates the need for additional finishing work at the job site, speeding up the overall timeline for the project.
5. High-Performance Insulated Panels: Energy-Efficient Solutions
As the world places a greater emphasis on energy saving, high-performance insulated precast panels are growing in popularity. These panels provide excellent thermal insulation, which lowers energy consumption and helps to maintain constant temperatures inside structures.
The demand for energy-efficient buildings is growing, and infrastructure development projects are no exception. These insulated panels are ideal for commercial and residential projects, as they lower heating and cooling costs, making them a wise investment for anyone looking to build long-lasting, cost-effective structures.
In modular construction, using insulated panels further streamlines the building process. They are easy to transport and install, thereby reducing labour costs and installation times while offering the best performance.
6. Automation in Production: Speed and Precision
Automation improves the speed and accuracy of precast concrete production operations. Automation reduces human error and increases output in everything from robotic arms that fill molds to devices that manage curing.
For extensive infrastructure development projects, where accuracy and timeliness are crucial, this is extremely advantageous. Automation makes it possible to produce precast concrete components quickly, consistently, and reliably improving project management and cost control.
Moreover, automation frees up workers from repetitive tasks, allowing them to focus on more skilled areas of production, further elevating the overall quality of the work.
7. Modular Construction: The Future of Faster Builds
Modular construction redefines how we think about buildings. Rather than traditional construction, where each part of a building is constructed from scratch on-site, modular construction involves the off-site fabrication of prefabricated concrete components assembled on-site.
This method is transforming the precast concrete industry, as it reduces both construction time and labour costs. The project timetable can be greatly accelerated by, for instance, building full office floors or housing units off-site in a fraction of the time.
This approach particularly benefits large infrastructure development projects, where time and efficiency are crucial. By using precast concrete in modular construction, companies can build faster, with fewer delays, and maintain high quality throughout.
8. Digital Twin Technology: The Power of Virtual Models
The rise of digital twin technology allows contractors and engineers to create virtual replicas of buildings and infrastructure projects. These digital models provide real-time monitoring and performance analysis by accurately simulating every aspect of the physical structures.
For producers of precast concrete, this translates into more precise modeling of structural components, which improves design, speeds up manufacturing, and reduces errors. Because it enables teams to model a building's lifecycle from construction to eventual demolition or rehabilitation, it is an effective tool in infrastructure development.
In large-scale modular construction projects where accuracy is crucial, digital twins are quite useful. This technology ensures easier, more efficient building by enabling teams to foresee issues before they arise.
9. Expanding Markets: Global Growth in Precast Concrete
The precast concrete industry is seeing rapid growth in emerging markets, driven by urbanisation and infrastructure needs in developing regions. Countries in Asia, Africa, and Latin America increasingly adopt modular construction and precast concrete due to their cost-effectiveness and faster build times.
Businesses have an increasing chance to access these markets as more governments make investments in extensive infrastructure development. Cross-border cooperation and new revenue streams are made possible for companies in the precast concrete industry by the global expansion.
This expansion aims to promote innovation and cross-border exchange of best practices in addition to increasing business opportunities. The precast concrete sector will develop as these markets expand, providing even more opportunities for innovative ideas and environmentally friendly building practices.
Summing Up!
The future of construction is being redefined by the trends influencing 2025, and the precast concrete industry is changing quickly.
Processes are becoming faster, more environmentally friendly, and more economical thanks to advances like 3D printing and modular construction. Companies that adopt these adjustments will be well-positioned to lead and promote projects that use cutting-edge technologies and environmentally responsible practices.
Precast concrete has a bright future, and staying on top of these developments will help you take advantage of the opportunities and overcome the obstacles that lie ahead.